Production Process for High-Performance Ceramics
The production of high-performance ceramics begins with the selection and preparation of the raw materials. These ceramic masses are pressed into moulded parts or shaped by other processes such as extrusion, injection moulding, casting or 3D printing. After green machining and mechanical processing of the ceramic blank, these blanks are debinded. Depending on the sintering conditions (primarily the atmosphere), debinding can be part of the sintering process or, as with aluminium nitride, it can be carried out as a separate step beforehand. Finally, the sintering itself takes place. During this process, the material is compressed and solidified at high temperatures, giving it its final properties. Finally, the components are precisely machined by grinding, polishing or other finishing steps.
Discover the fascinating step-by-step process of manufacturing technical ceramics – or sit back and learn about the entire process in detail in our explanatory film.
1 Powder & Mass Preparation
- Raw material selection
- processing: addition of additives | grinding | mixing | granulating | drying
In the powder & mass preparation, powdery raw materials as well as organic and inorganic additives are mixed and prepared for the subsequent moulding process. For example, the subsequent properties of the ceramic can be specifically influenced by grinding.
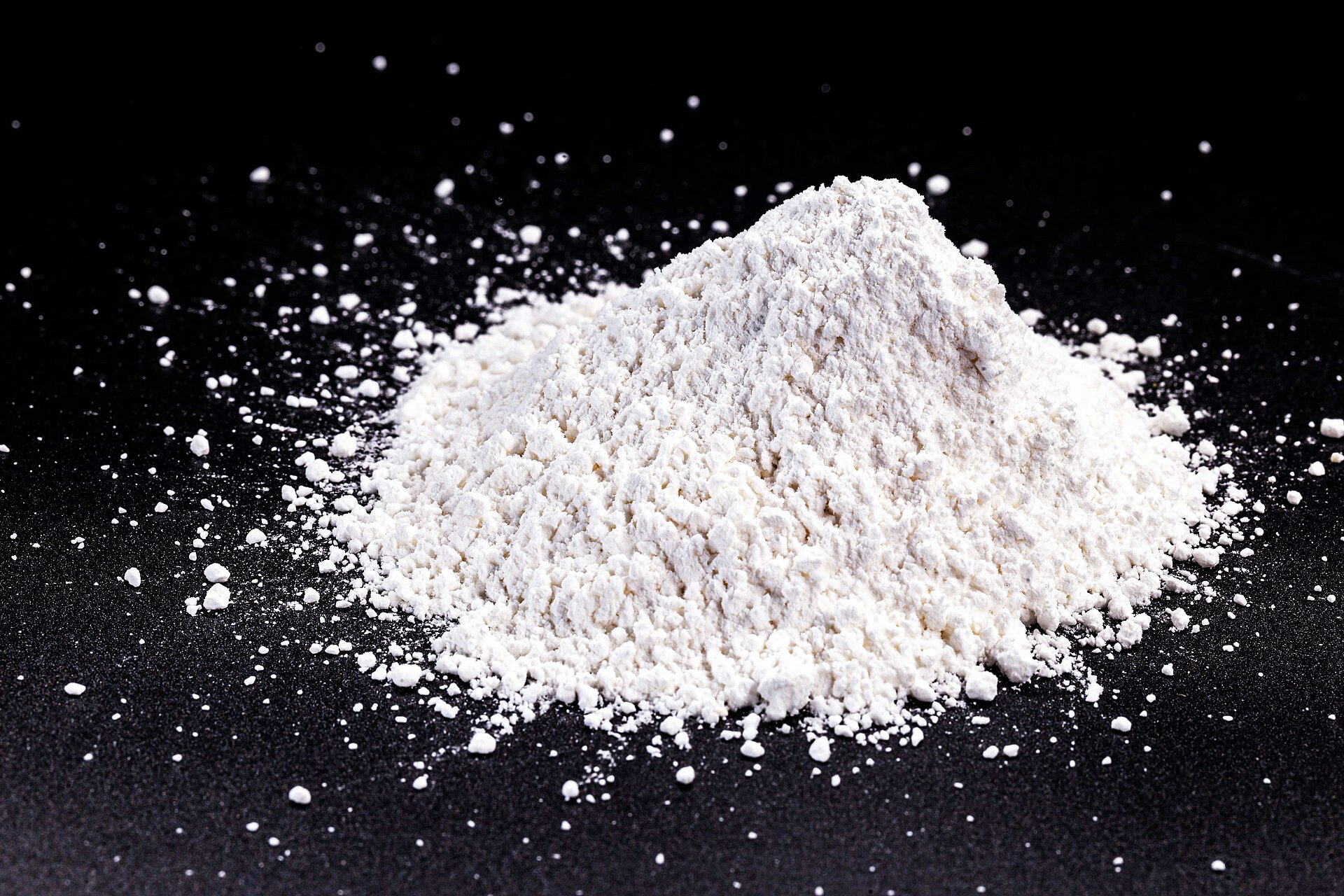
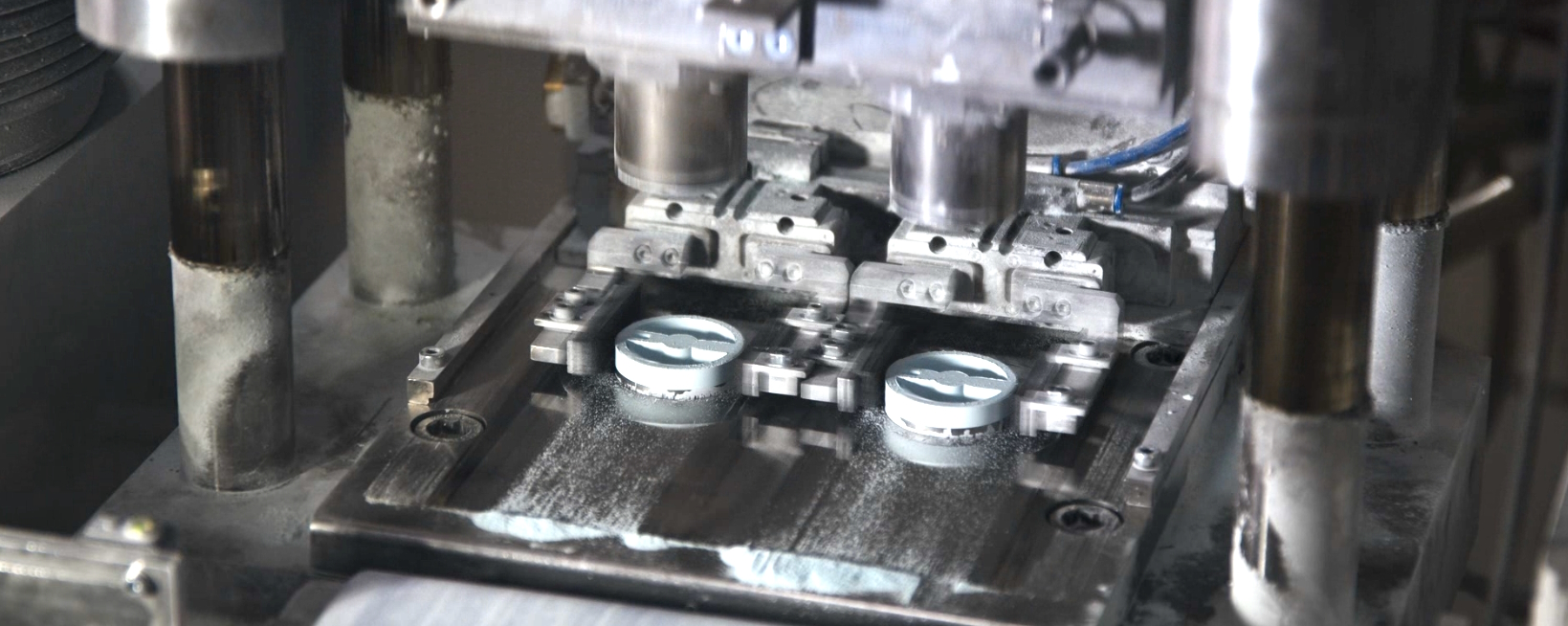
2 Shaping
- Pressing: Isostatic pressing | Axial pressing
- Injection moulding
- Extrusion
- Casting: Tape casting | Slip casting
- 3D printing
The ceramic mass is shaped into the desired geometry by processes such as pressing, casting or extruding. In this process, the material is solidified to such an extent that a low level of adhesion is created between the particles and the component can be further processed.
3 Green Machining
- Mechanical processing: milling | turning | drilling
- laser cutting
- stamping of foils
- cutting of extruded materials to length
Green machining is the mechanical processing of the ceramic blank in its unfired, so-called ‘green’ state. In this stage, the material can be processed relatively easily and cost-effectively due to its low strength. Among other things, processes such as grinding, milling, lasing, punching or drilling are used.
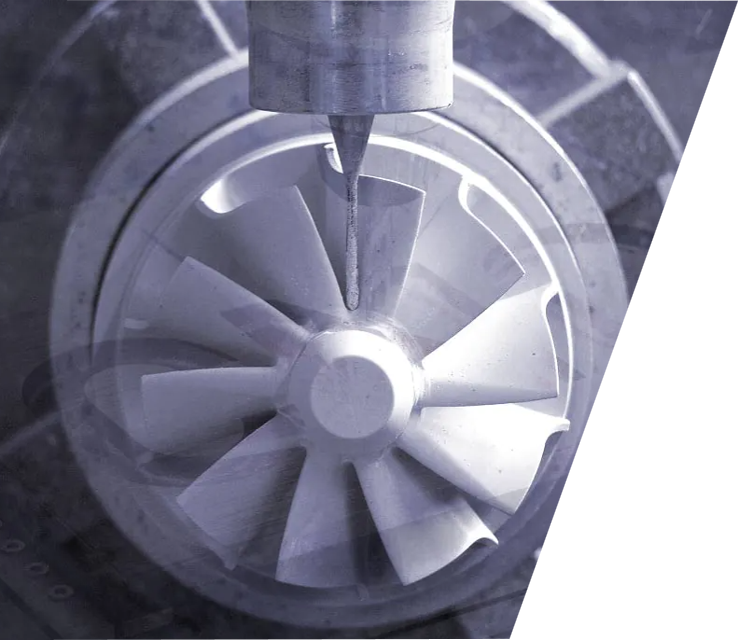
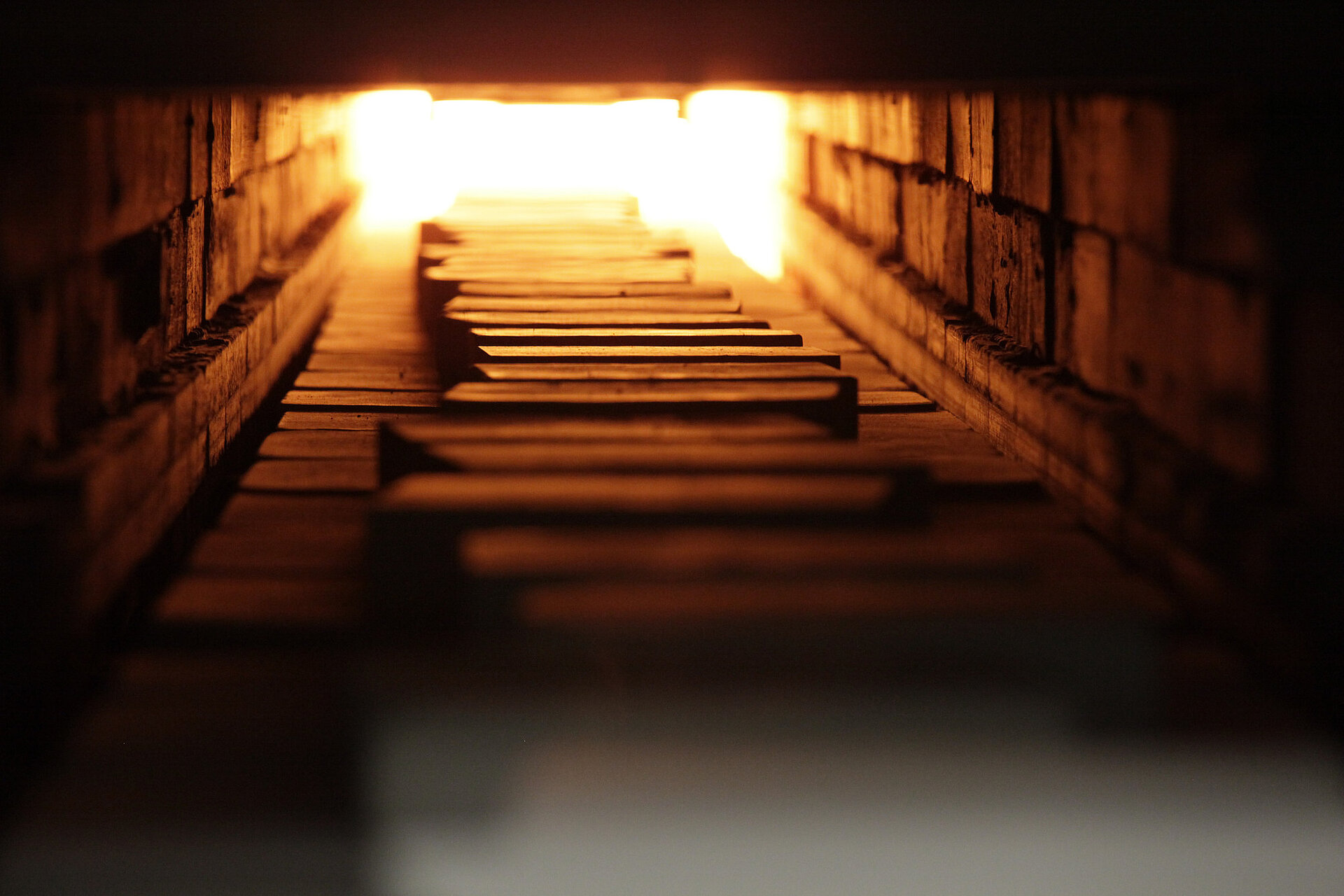
4 Sintering
- Sintering method: Pressureless | with pressure
- Sintering process: continuous | discontinuous
- Atmosphere: air | inert gas | vacuum
- Sintering temperatures
During sintering, the material is compressed and solidified at high temperatures below the melting point, creating a ceramic bond. In this process, the particles combine to form a solid structure, whereby the desired final properties are achieved. Depending on the material, different processes and furnaces are used, which differ in terms of temperature, firing time and atmosphere. Depending on the sintering conditions (especially the atmosphere), debinding may be part of the sintering process or, as in the case of aluminium nitride, may be carried out beforehand as a separate step.
5 Finishing
- Grinding
- Lapping
- Polishing
- Lasering
Final machining is only carried out for particularly demanding requirements, because the high strength of the material means that machining after sintering is much more complex. Final machining includes precise mechanical processing steps such as grinding, polishing and drilling to achieve tight tolerances and smooth surfaces.
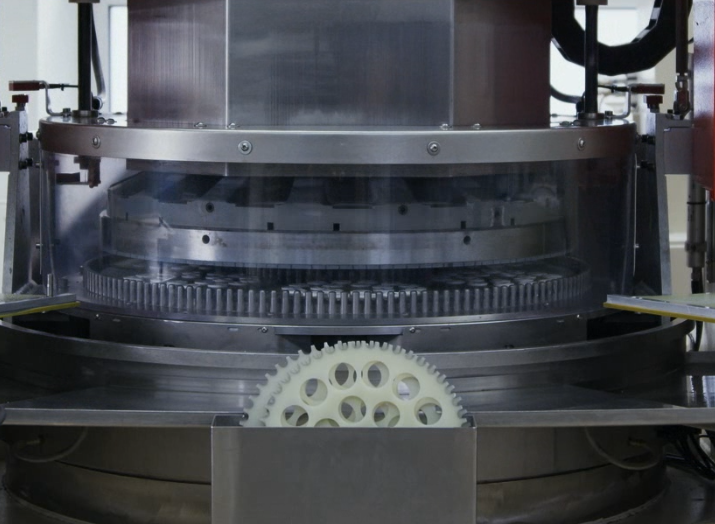
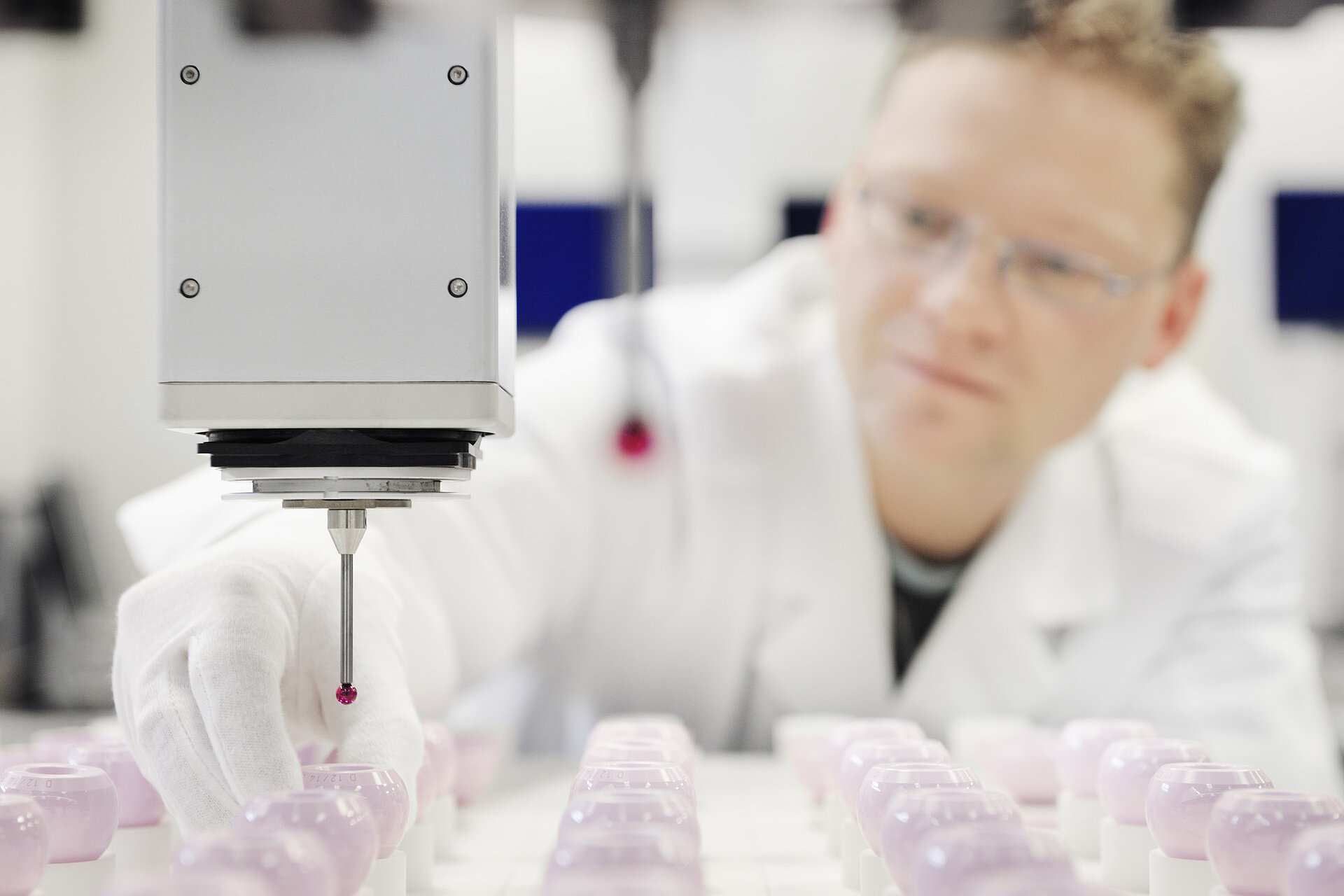
6 Final Inspection
The final inspection includes checking the finished ceramic parts for dimensional accuracy, surface quality and possible defects such as cracks or unwanted porosity.
This inspection is usually carried out by visual inspection, measurements and, in some cases, non-destructive testing methods to ensure that the products meet the specified requirements.