Ceramic Substrates
A wide range of different key components for electronic applications (e.g. electronic circuit carriers) can be manufactured from ceramic substrates, which fulfil their function permanently and safely in various Areas of Application(Link to the overview on our global website).
In cooperation with our team in Europe, we at CeramTec North America offer you a wide range of solutions for your specific requirements, whether medical technology, telecommunications, consumer electronics, electromobility or power generation - ceramic substrates are used everywhere due to their thermal, mechanical, insulating and chemical properties and enable us to network our world and drive modern technologies forward.
CeramTec North America is your One-Stop-Shop for all common ceramic substrates and offers everything from a single source: aluminium oxide, aluminium nitride (with a bending strength of 450 Mpa), zirconium toughened aluminium oxide ZTA, zirconium oxide ZrO2 and in the course of 2024 also silicon nitride.
In addition to the ceramic substrates, this also includes engineering as well as laser processing and metallisation of the substrates. The comprehensive one-stop-shop portfolio of ceramic materials enables our customers to source all major ceramic substrates from a single manufacturer, supplement them as needed and streamline their supply chains.
Our ceramic substrates are characterised by a high packing density in terms of size and weight, which is achieved through their excellent ampacity, thermal conductivity and efficient heat spread with a thick copper metallisation by the customer.
At the same time, the low specific weight is maintained due to the low bulk density of the ceramic compared to, for example, metal. This makes our ceramic substrates the optimal choice for demanding applications where efficiency and performance are paramount.
Outstanding thermal conductivity of our ceramic materials, such as aluminium nitride (AlN), aluminium oxide (Al2O3), zirconium oxide-aluminium oxide (ZTA) and silicon nitride (Si3N4).
Thanks to the extraordinary lattice vibrations in ceramics (phonon resonance), they achieve remarkable heat dissipation compared to plastics. These properties make ceramics a first-class choice for heat-sensitive applications.
The excellent suitability for use in the high frequency range is ensured by a low dielectric loss factor or tan delta of the ceramic materials. A low dielectric loss factor is essential to ensure that the material has minimal energy loss and low attenuation effects on high frequency signals. This leads to improved efficiency and performance of high frequency components and systems.
Lasered and Metallised Substrates
At CeramTec, we manufacture and process ceramic substrates using various processes depending on the application, material, geometry and number of pieces: From punching, lasering and dry pressing to various hard machining processes.
In addition, we also metallise the substrates ourselves, making them ideal for direct assembly with electronic components. The metallisation pastes are developed by ourselves and are characterised by high adhesive strength, good solder flow and excellent resistance in solder baths. In the process, a conductive layer is applied to the substrate to create the conductor paths and connections for the electronic components and to protect the substrate from corrosion or other environmental influences.
RoHS Certification
A key prerequisite for CeramTec’s successful partnership with the electronics industry is the ability to deliver the right materials.
CeramTec offers the world’s top ceramic materials for thick and thin film technology and provides ceramics optimally designed to meet your specification profiles.
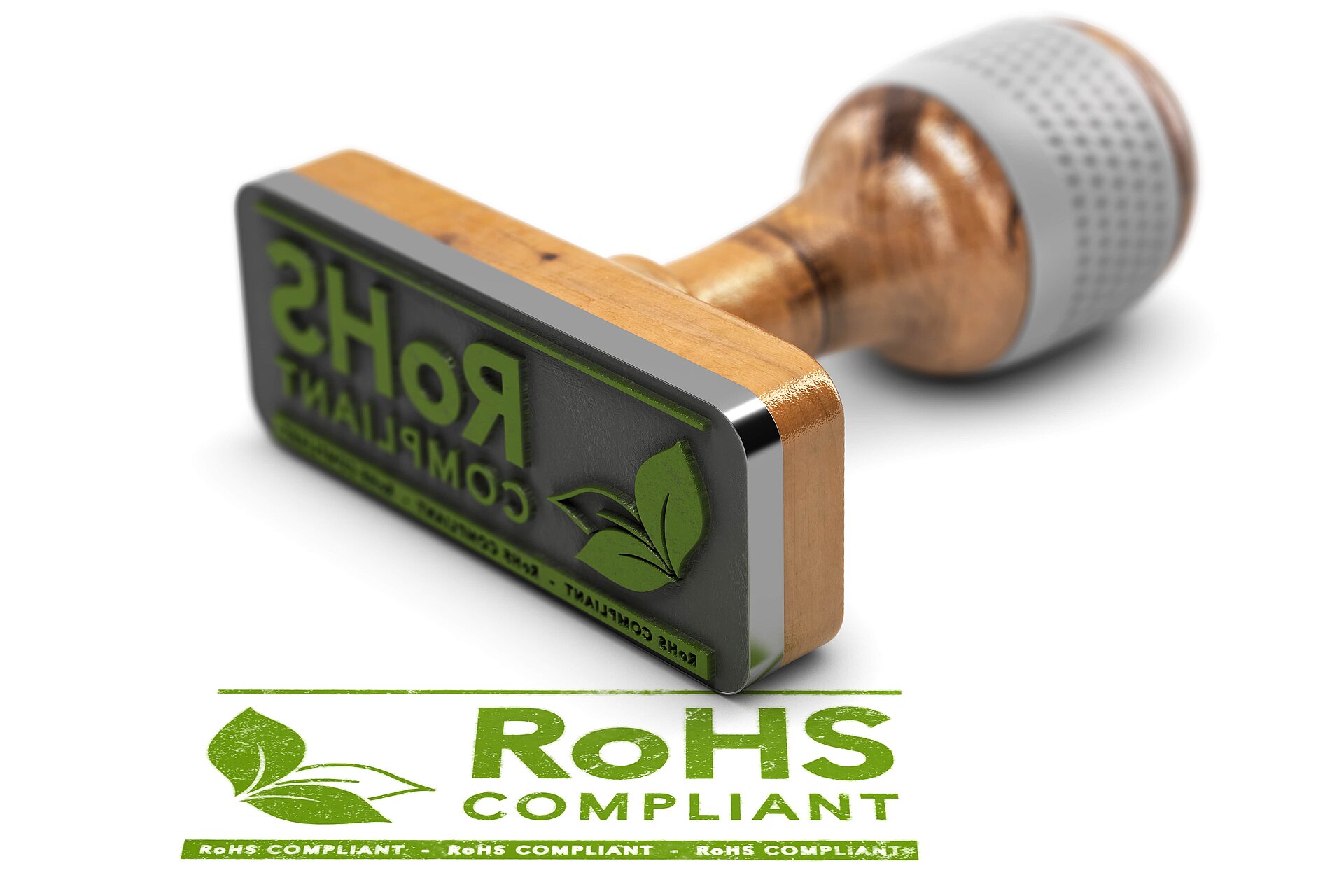
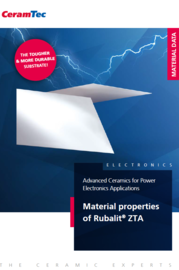
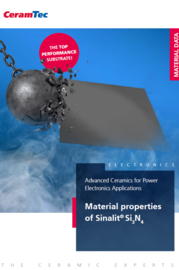
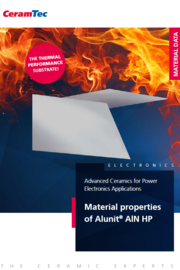
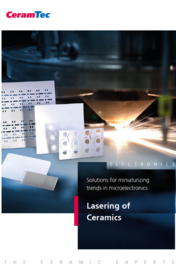
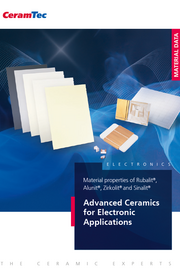